Cutting-Edge Aerospace Metal Forming Technologies
We stand by your side!
To our clients and friends,
On behalf of Aries Alliance and Cyril Bath Co., please know that our customers, integrators, suppliers and employees are our first priority during these difficult and ever changing times.
Cyril Bath is designated as an essential business/critical infrastructure supplier in several industry categories under the Department of Homeland Security’s Federal Cyber and Infrastructure Security (CISA) program. CISA program guidance indicates our special responsibility to maintain our normal work schedule in support of our critical clients.
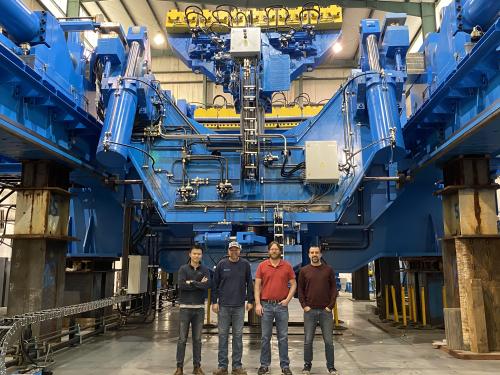
Aries Industries
Companies
Cyril Bath is part of Aries Industries, a group including companies with acknowledged expertise in the field of metal shaping machines and aerospace part production. Our global presence allows us to better meet the demands of our international customers.
Sheet Stretch Forming
Our stretch forming machines allows the manufacture of large parts. They are engineered for safe operations and unparalleled repeatability.
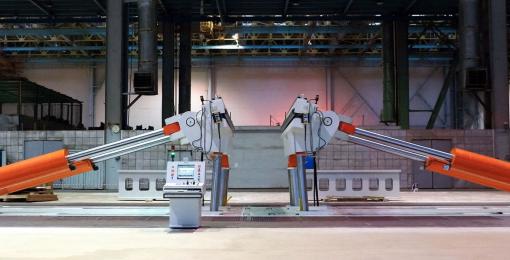
Profile Stretch Forming
Tailored to your specifications, our FEV & V presses allow you to form complex shapes while offering accuracy and repeatability.
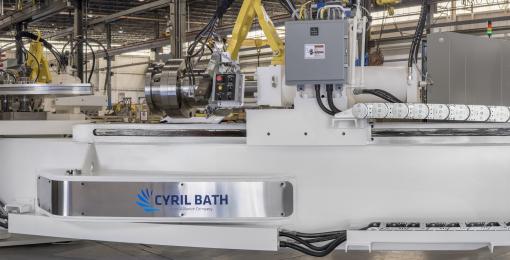
Elastoforming
Elastoforming presses allow high manufacturing flexibility and are well adapted for your small and medium series manufacturing.
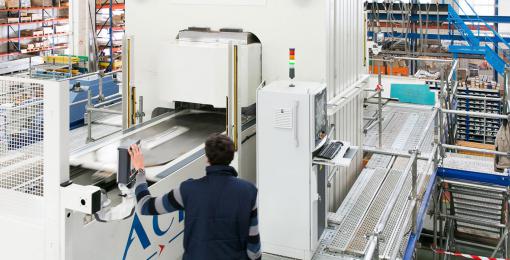
Hot Forming
Our Hot Forming presses are designed to answer your productivity challenges. Together, we work from your press requirements to design a unique manufacturing means.
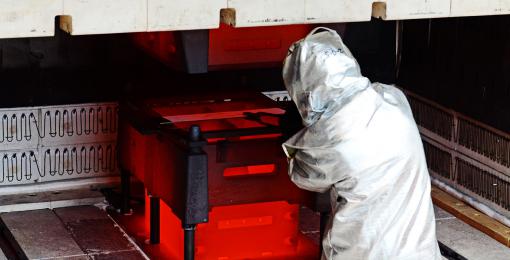
FSP Press
Cyril Bath has been perfecting the design of superplastic forming (SPF) presses for decades, having supplied 100+ presses to manufacturers in the aerospace industry.
These presses are a staple of Cyril Bath’s portfolio of metal forming equipment.
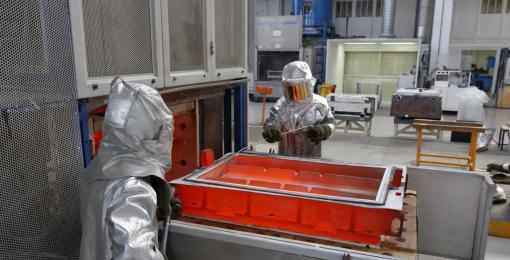
Automated Turnkey Solutions
Our unique expertise and know-how in the metal forming processes and part manufacturing led us to add workcell and workshop engineering to our offer. Cyril Bath can supply turnkey customized solutions, from advice and planning through installation and training taking into account :
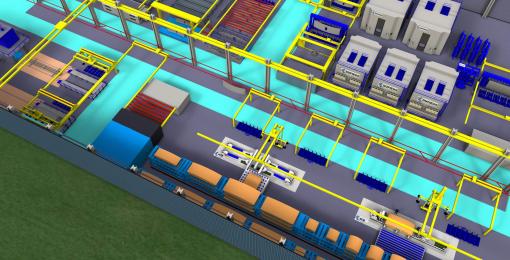